Have you ever wondered how ceramics are made? Artisan and practical ceramic products have been around for centuries, with the majority of the modern age starting right here in Stoke-on-Trent, dubbed ‘The Potteries’ and those from Stoke-on-Trent as ‘The Potters’.
Here is a (not so simple) step-by-step on how the English Ladies Co. created ceramic replicas of some of the most famous characters in Charlie Bears’ history:
1. Design
Our design director, Mal, took lots of images and textures as inspiration in order for Charlie Bears to be brought to life in ceramic form! She took care when including their fashionable accessories and curious expressions. The dimensions, colour codes and sculpting methods were thoroughly thought through before any material samples were created.
2. Modelling
The original, furry Charlie Bears are fabulous models already, so sitting still whilst our 3D designers created the clay structure was a walk in the park! Did you know that the first clay models are 14-20% bigger than the finished piece, as the water content of the clay evaporates in the kiln!
Furthermore, all of our pieces are made in multiple parts called ‘undercuts’ – they cannot be made as just one model as this creates a risk for cracks. In addition, using the undercuts help to achieve a precise finish. This was especially important in order to ensure the jointed bears had all of their joints defined!
Below you will be able to see how many parts were made for each bear, before they are assembled to make up the master mould of the complete form.
3. Casting
Luckily for these 5 Charlie Bears, they all got to be cast as lead roles for this ceramics collection!
Casting, or slipcasting, in the ceramics world actually means when liquid clay is poured into the master mould to create a hollow form that will then go on to be fired in the kiln. When we cast pieces from original master-moulds we cap their use at 30 times.
The average use per master mould is 30-50 but the ELC always stop at 30 because each time the mould is used it becomes softer, so the details are less defined the more it’s used. Therefore, to make 600 pieces of our Charlie Bears, means 20 sets of master moulds used, per bear. The process of making ceramics is lengthy and expensive right from the beginning! You’ll find on some cheaper products that the definition is not high quality because it costs more to make it.
4. Firing
Once you have a soft mould of the figurine, it needs to be heated up to become strong and sturdy!
The first fire of the mould is called the ‘biscuit’ fire because it has a rough texture. It is then dipped or sprayed in liquid glass (glaze). It is really important not to glaze the figures too thick as it will fill in all the details from the mould. Likewise if it is not thick enough, the heat will get through and create black ‘burn’ marks over it. There is a real art and precision to how much glaze is dipped, and this is all produced to perfection by hand. The piece is then fired in the kiln again for the second time, in order to set the glaze in place.
5. Colour
Next, we build the colours up. This process is hand-painted, using precision and master skill to apply just the right amount of paint for each turn in the kiln. It might be that to create certain colours they need to be painted and fired in separate stages, such as the lighter colours and darker colours consecutively – or some colours will simply need more fires than others. It has to be mathematically organised.
When we use the 22ct gold or platinum (such as on Frost’s bell), or lithography for the eyes or backstamp etc., they are all fired at a lower temperature. Each of our pieces are fired for a minimum of 4 times in the electric kilns.
Can you guess how many parts, colours and fires each of the bears needed?
*Answers are below!
Every piece from the English Ladies Co. is handmade and hand-decorated by skilled craftsmen and women using the finest materials. We only operate in small-batch production runs of 300 pieces a time. This means that not all 600 bears will be made at the same time – and in the future some bears could be made in different years, meaning different year-marks!
The process of creating our beautiful ceramic giftware can be extremely lengthy, and tricky to edit further into the process. That is why it is so important to get the first step right.
Shall we take a look at the individual bears journey?
Jake
- Mould parts = 8
- Colours = 7
- Total fires = 5
- Height = 17cm/ 6.7”
Our Jake figure is made up of 8 individual parts, which are assembled when the clay is still wet, to create our delicate figure. He sits atop an old briefcase inspired by the Charlie Bears pin badge case!
Jake is fired once to biscuit (when the ceramic hardens) and once after glazing, to create the shiny surface that the English Ladies brand is known for. The paint is then applied in 3 layers, and fired in between each layer, to give the beautiful effect of the fur.
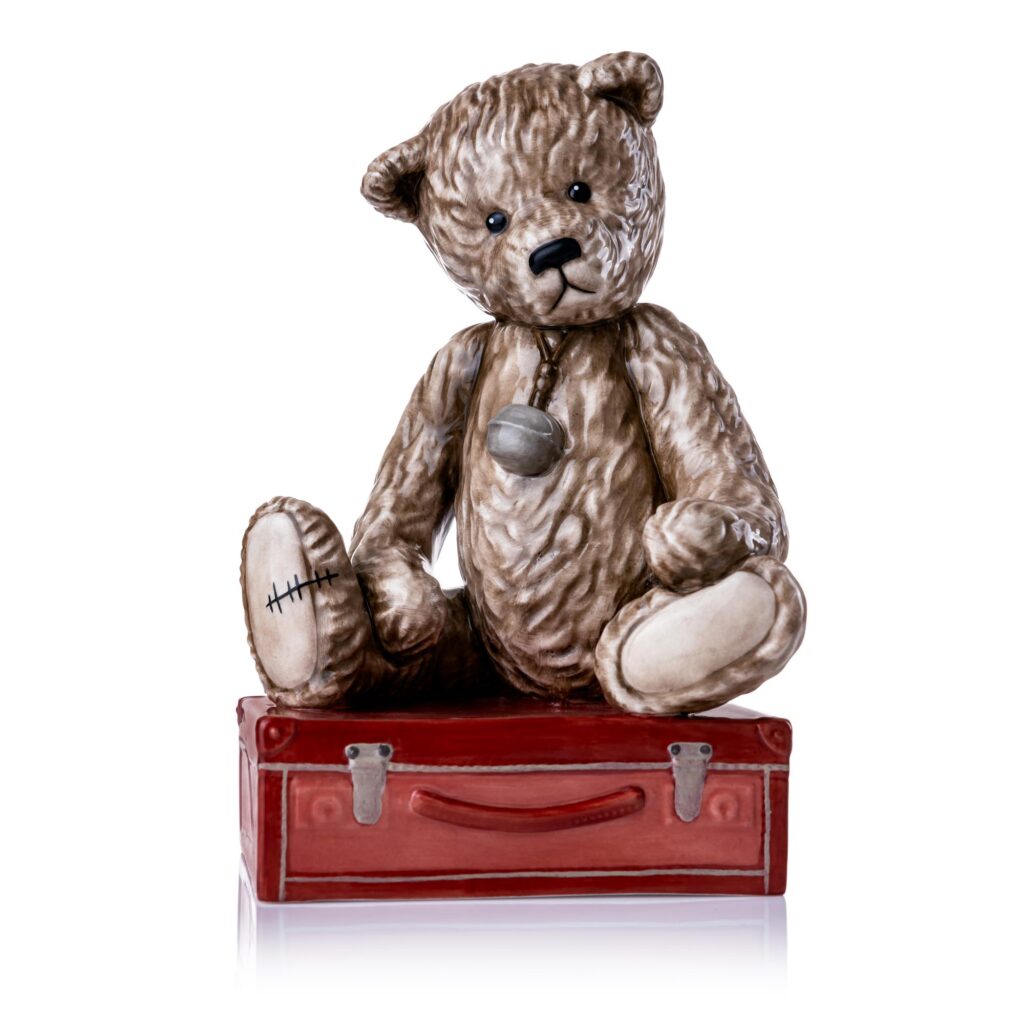
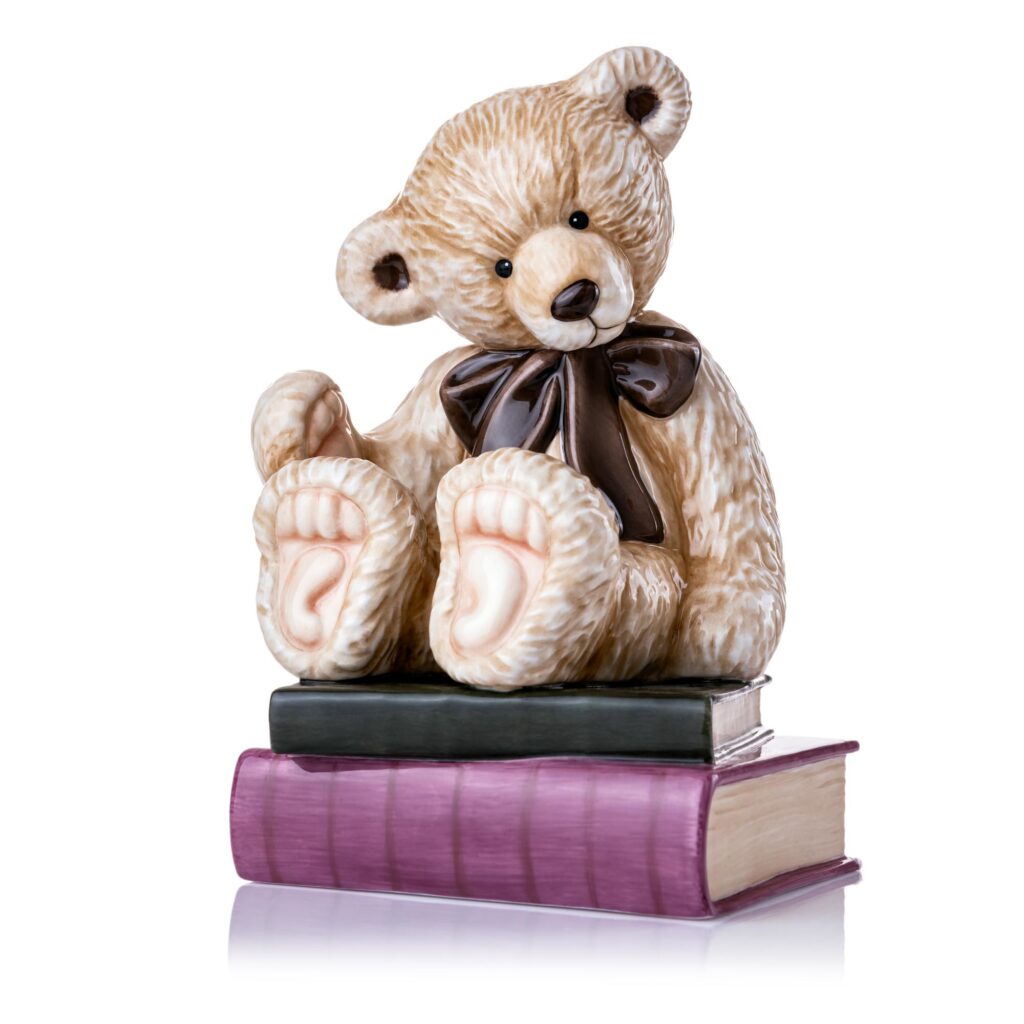
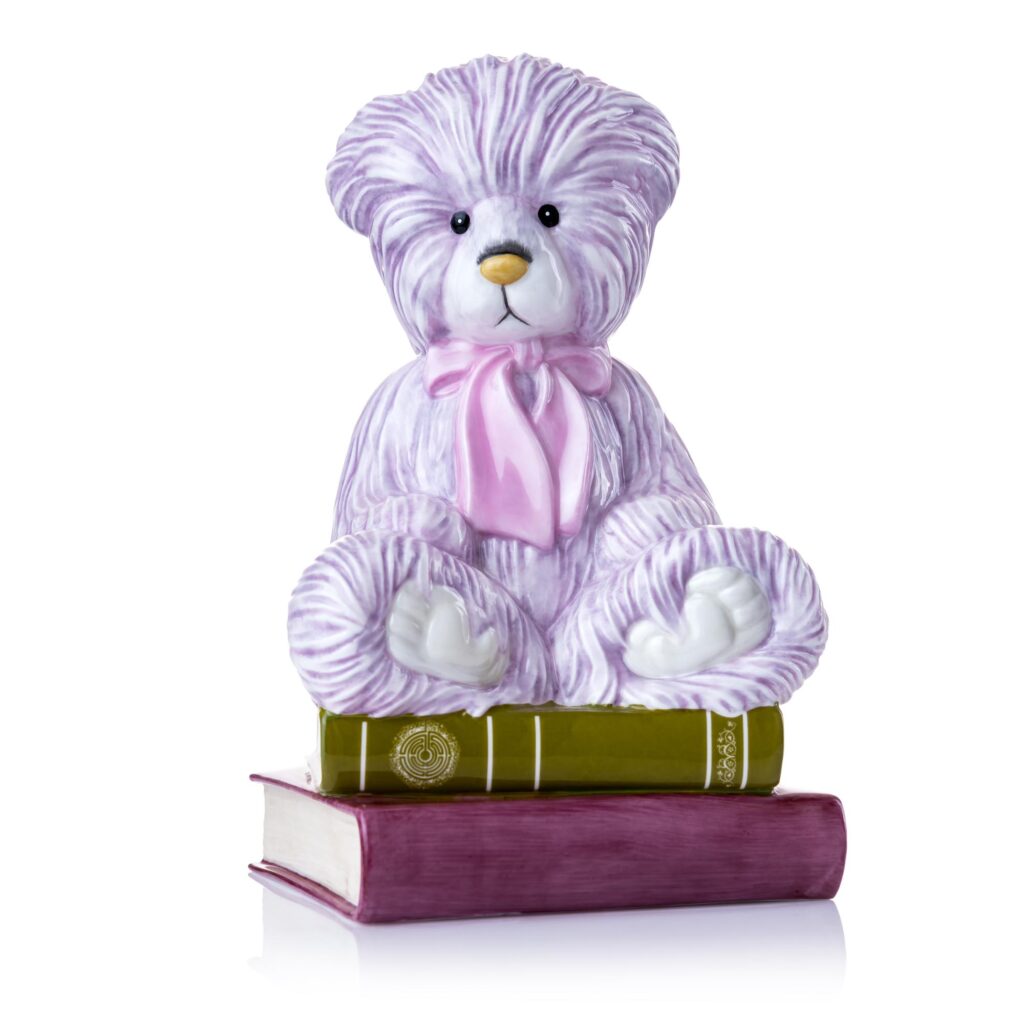
Charlie Year Bear 2009
- Mould parts = 5
- Colours = 7
- Total Fires = 5
- Height = 17cm/ 6.7”
Charlie Year Bear 2024
- Mould parts = 4
- Colours = 10
- Total Fires = 5
- Height = 18cm/ 7.1”
It can take up to 12 months to model, develop and manufacture our pieces, so we have been part of the 2024 Year Bear secret for some time! As soon as the images were released, we set about creating the figure. At once we noticed that the colours are much more varied than the first Year Bear! We needed 10 ceramic colours for this piece!
Frost
- Mould parts = 7
- Colours = 13
- Total fires = 5
- Height = 15.5cm/ 6.1”
Frost is one beary special Hatty Bear, as the silver bell at the end of his hat is actually painted in real platinum! When applying these metallic elements, the kiln needs to be set at a lower temperature for best results.
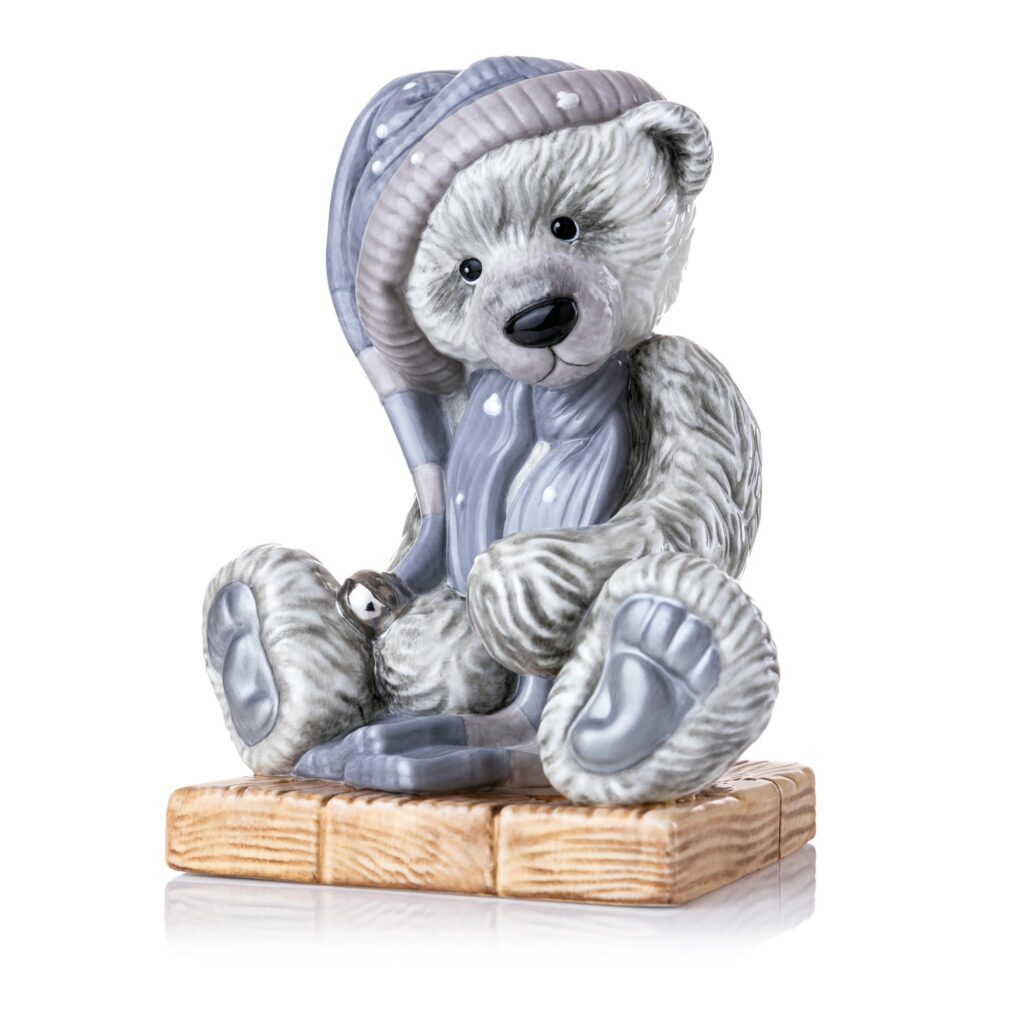
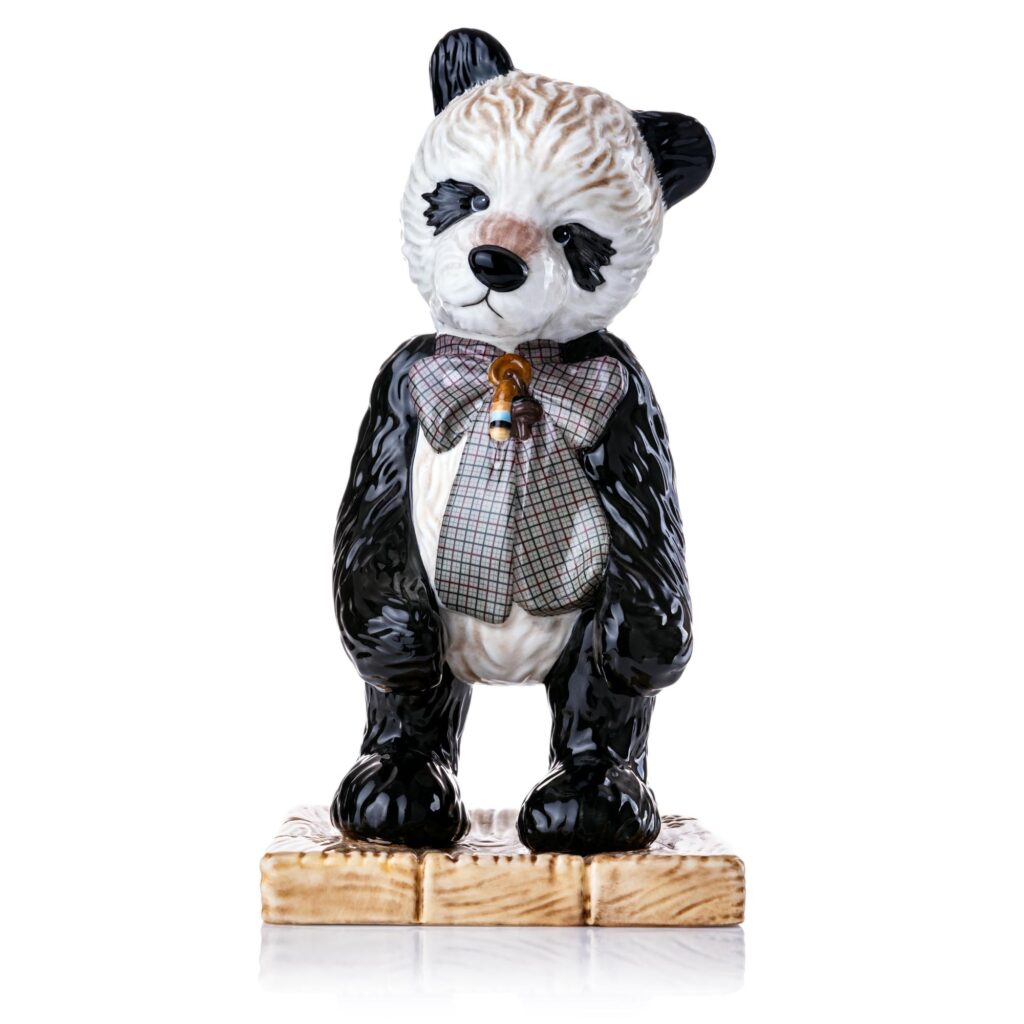
Mr Widget
Mould parts = 7
Colours = 13
Total fires = 5
Height = 20.5cm/ 8”
As the tallest of the first 5 bears, Mr Widget has been assembled in 7 mould parts to ensure a stable position. His stance sure creates an eye-catching centrepiece!
We hope you now have more knowledge about how intricately these ceramic bears are made.
Happy collecting!